Jetfixer
Well-known member
So I had my brake light switch fail on my 2020 RTL. Even though it's under warranty, no one near me had one in stock. So I ordered one from a dealer in VA. No problem. Unfortunately, most of the right side body panels must be removed to access the switch connector. The switch itself is easily reached without removing anything. However, in another shocking example of very poor engineering, the round switch has two nuts threaded on its body and appears to go through a bracket. It doesn't. The bracket is more like a fork shape that is open at the BOTTOM. If either of the two nuts vibrates loose, the switch will simply fall out and hang by its wires and the spring that pulls the plunger. That is absolutely unforgiveable. If they couldn't have the body of the switch captured completely (which they could have), then at least the fork should not be pointed down, which would also have been possible.
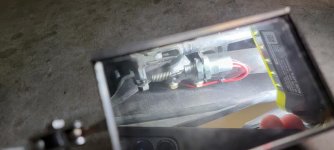
View looking up using a mirror. You can see the bracket is open at the bottom.
As a footnote, the switch that is still shown on all of the online parts catalogs has been superseded. No obvious difference, but perhaps internal changes.
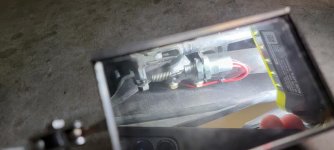
View looking up using a mirror. You can see the bracket is open at the bottom.
As a footnote, the switch that is still shown on all of the online parts catalogs has been superseded. No obvious difference, but perhaps internal changes.
Last edited: