First, Ron, your empirical testing is better than any textbook study. Many have tried your torsion/anti-sway bar and many prefer them to the OEM torsion bars.
To clarify, though, the steel type doen't affect the spring rate. That's an inherent property of the steel listed as E, or Young's Modulus, or flex modulus. The spring rate is relatively consistent across steel types @ 30,000,000 psi. The steel type and hardness affect the yield point of the steel alloy. For a spring to function, deflect and return to the original position, the flexure must be in the elastic proportional range of the steels performance.
Geometry comes into play for sheer and tensile stress maximums. Maximum stress normally occurs in the outter layer/skin of the structure. Bending and shear-related failures initiate at points where the stress properties have been exceded, due to deflection or geometric concentrations.
Here's an article that discusses stiffness, flex modulus, relative to hardness, for knife makers:
https://knifesteelnerds.com/2018/03/13/why-doesnt-heat-treating-affect-steel-flex/
This article talks about steel properties:
https://engineeringdiscoveries.com/what-are-the-properties-of-steel/
This is an image from the article, which depicts stress/strain curves for a number of steel types. All 6 curves have a common start, their elastic proportional range. As long as the load, given the same geometry, is within that range, the steel will deflect and return to its original position.
Where each curve begins to deviate from that straight line, defines its yield point. All 6 curves are at different stress levels. That's where the steel affects the ability to return to its initial geometry. The purple line is about 23% of the strongest steel on the chart. As long as the deflection, represented as strain, is under the yield points, each has the same spring constant.
Yes, geometry will affect maximum stress in the design, and must be considered if one is changing a design. Geometry all affects Moment of Inertia, I. It has a n^4 power effect on torsional resistance as this part is designed: small changes in diameter can significantly affect apparent stiffness. Going from 9/16" to 3/4" diameter will nearly double the resistance. I don't have the calculations in front of me to quote exact numbers.
Steel type also drives cycle life and fatigue life of an article. So, yes, steel type is important. However, the spring rate doesn't change.
Bottom Line: you have the empirical test data which supports your targeted improvements, providing less tilt of the Spyder going through a corner.
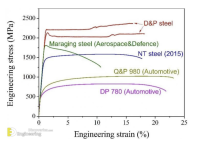