Today was quiet contemplation day. Just kidding, it was cleaning up the mess I've made in the last three projects so I could actually work in the barn again. Once it was clean it was time to mess it up again, naturally. The other day a buddy and I were talking about how pitiful the stock horns are on bikes, and I've recently had quite a few opportunities to use mine and agreed. I had a wolo big boy horn on hand for reasons, so I figured I'd see if it would fit in the bike. Short answer is yes, long answer is yeeeeeeeeeeeeeeeeeeeeeeeeeeeeeeeeeeeeeeeeeeeeeeesssssssssssssssssssssssssssssssssssssssssss. Barely. I started out trying to work through the side of the bike where the stock horn is, but that way lies madness. Ended up picking the whole shebang up on one of my craftsman motorcycle lifts and working on it from underneath.
Untitled by Uncle Grr!, on Flickr
Once I removed the stock horn and it's bracket, I was able to assess how much space I had to work with. Basically the size of the wolo plus a tiny bit. Here's the beginning of the bracket I made for it. Used some old stainless shelf a neighbor gave me.
Untitled by Uncle Grr!, on Flickr
I ended up bending it a few more places, and cutting some more off it for clearance, and painting it black because why not.
As stated, the wolo is in fact a big boy (that's grande boy for the metric folks) and had to be clearanced quite a bit to fit. Sanded off one side of the plastic body and part of the horn.
Untitled by Uncle Grr!, on Flickr
Drilled a hole in the back (didn't go into the horn part) to clear a suspension bolt.
Untitled by Uncle Grr!, on Flickr
And the bracket installed to the horn, locktited.
Untitled by Uncle Grr!, on Flickr
Here it is installed, looking up from underneath.
Untitled by Uncle Grr!, on Flickr
And here is all you can see
Untitled by Uncle Grr!, on Flickr
For wiring, I decided that I could just reuse the stock wires and figured it'd be fine. I couldn't even finish the thought before I said no. The stock horn doesn't have it's own fuse, it appears to be covered by the 'load shedding' circuit fuse, so if I blew that (no pun intended) I'd lose a lot of other stuff. So I added a relay (left side) that's activated by the stock horn wires, gets power from the battery directly (wire going across the front of the battery, fuse is under the rubber battery hold-down strap). Now it's much better and significantly louder, and has it's very own 15a fuse. I laid on it for about 30 seconds to break the horn in, and didn't blow the fuse so I call it successfull. Oh I also drilled three 1" holes in the plastic splash guard directly below the horn to let the music free. And once again, it fit my requirements of being done entirely with stuff I had on hand.
Untitled by Uncle Grr!, on Flickr
Oh yeah, I did it all while it was up on the lift and turned the bars side to side throughout the process so worst case scenario, even if I'm jumping and turning full lock, I still have clearance around the horn.

Once I removed the stock horn and it's bracket, I was able to assess how much space I had to work with. Basically the size of the wolo plus a tiny bit. Here's the beginning of the bracket I made for it. Used some old stainless shelf a neighbor gave me.

I ended up bending it a few more places, and cutting some more off it for clearance, and painting it black because why not.
As stated, the wolo is in fact a big boy (that's grande boy for the metric folks) and had to be clearanced quite a bit to fit. Sanded off one side of the plastic body and part of the horn.

Drilled a hole in the back (didn't go into the horn part) to clear a suspension bolt.

And the bracket installed to the horn, locktited.

Here it is installed, looking up from underneath.
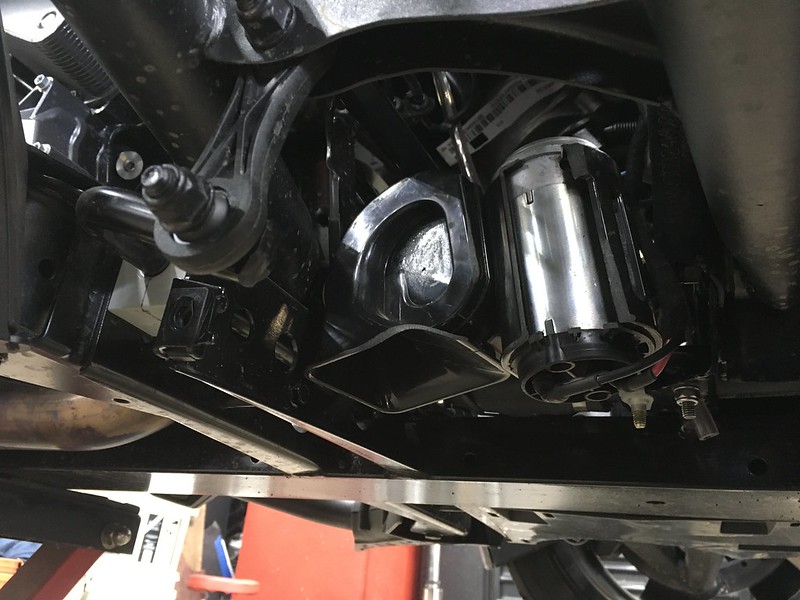
And here is all you can see

For wiring, I decided that I could just reuse the stock wires and figured it'd be fine. I couldn't even finish the thought before I said no. The stock horn doesn't have it's own fuse, it appears to be covered by the 'load shedding' circuit fuse, so if I blew that (no pun intended) I'd lose a lot of other stuff. So I added a relay (left side) that's activated by the stock horn wires, gets power from the battery directly (wire going across the front of the battery, fuse is under the rubber battery hold-down strap). Now it's much better and significantly louder, and has it's very own 15a fuse. I laid on it for about 30 seconds to break the horn in, and didn't blow the fuse so I call it successfull. Oh I also drilled three 1" holes in the plastic splash guard directly below the horn to let the music free. And once again, it fit my requirements of being done entirely with stuff I had on hand.

Oh yeah, I did it all while it was up on the lift and turned the bars side to side throughout the process so worst case scenario, even if I'm jumping and turning full lock, I still have clearance around the horn.