WilcoJunoHotel
New member
I saw these pictures on the web and I thought I would post them here as clarification for how the axle adjusters work on the Spyder RT.
I am a visual kind of person and if I can visualize what I am doing while working on something then I understand what is going on and it is not just trial and error when trying to fix something.
The photos show the swing arm caps (black gizmo) and shims which are used to adjust the axle. The shims are what is inside the swingarm and the caps are what you see at the back of the swingarm.
The caps have screws which have nuts that are "captured" between the 2 flat shims (2 on each side of the swingarm). If you look closely at the pics, you can see where the nuts nest into the shims.
When you adjust the screw it will move the shim; However, the swing arm cap is part of the assembly so you can see why it is critical to keep the cap snug to the back of the swingarm at all times. If you don't then you can see that the shims can move because the screw is no longer tight to the cap and the shim and axle are free to move. This is why you need to tap the axle back and forth - those shims are fixed to the axle by the thru hole in the shim. I also take a dead blow hammer and tap on the caps to ensure that they are snug. Just a small bit of movement of those caps means the axle could move which would throw your belt adjustment off.
I suspect that the swingarm is sort of "flayed out" or "sprung" at an angle and as you torque the axle down, it actually pulls the swingarms inward and it is this inward pressure that will move the axle (shims and all). You can account for this by making sure the caps stay snug as you tighten everything down.
To adjust: With the axle loose (minimal pressure on main axle nut), turning the swing arm cap screw clockwise (tightening the screw) pulls the shim and axle backwards; Turning the screw counterclockwise (loosening the screw) will move the axle and shim forward. After any adjustment, the swingarm cap must be put back SNUG to the swingarm and remain snug as you torque the main axle nut back down to full torque spec. If you don't touch either cap when doing a tire change, you shouldn't have to do any adjustment. (I put blue or green tape over the caps and screws before starting the wheel removal process.)
Hope this helps someone.
(Normally this type of adjustment is done by a threaded rod which locks the adjustment shim into place - only BRP can tell you why they did it this way - I guess it was less expensive.)
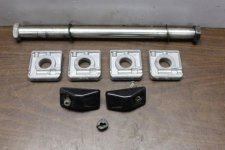
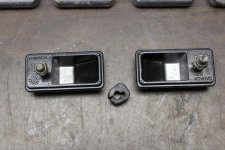
I am a visual kind of person and if I can visualize what I am doing while working on something then I understand what is going on and it is not just trial and error when trying to fix something.
The photos show the swing arm caps (black gizmo) and shims which are used to adjust the axle. The shims are what is inside the swingarm and the caps are what you see at the back of the swingarm.
The caps have screws which have nuts that are "captured" between the 2 flat shims (2 on each side of the swingarm). If you look closely at the pics, you can see where the nuts nest into the shims.
When you adjust the screw it will move the shim; However, the swing arm cap is part of the assembly so you can see why it is critical to keep the cap snug to the back of the swingarm at all times. If you don't then you can see that the shims can move because the screw is no longer tight to the cap and the shim and axle are free to move. This is why you need to tap the axle back and forth - those shims are fixed to the axle by the thru hole in the shim. I also take a dead blow hammer and tap on the caps to ensure that they are snug. Just a small bit of movement of those caps means the axle could move which would throw your belt adjustment off.
I suspect that the swingarm is sort of "flayed out" or "sprung" at an angle and as you torque the axle down, it actually pulls the swingarms inward and it is this inward pressure that will move the axle (shims and all). You can account for this by making sure the caps stay snug as you tighten everything down.
To adjust: With the axle loose (minimal pressure on main axle nut), turning the swing arm cap screw clockwise (tightening the screw) pulls the shim and axle backwards; Turning the screw counterclockwise (loosening the screw) will move the axle and shim forward. After any adjustment, the swingarm cap must be put back SNUG to the swingarm and remain snug as you torque the main axle nut back down to full torque spec. If you don't touch either cap when doing a tire change, you shouldn't have to do any adjustment. (I put blue or green tape over the caps and screws before starting the wheel removal process.)
Hope this helps someone.
(Normally this type of adjustment is done by a threaded rod which locks the adjustment shim into place - only BRP can tell you why they did it this way - I guess it was less expensive.)
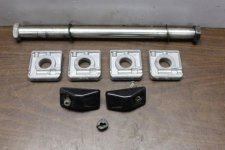
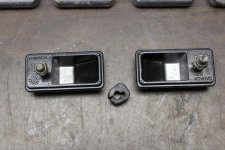
Last edited: