Sopher
Member
And 'Viola'. It's done. It's not shiny like an aluminum billet, but it sure is strong. This particular filament has 6000psi tensile strength.
I could easily print more and resell. Not sure how much to sell. Send me a PM if you're interested.
It took me a few hours to design, revise and perfect. The hardest part is getting the old one off. I chose to remove the small end with the magnet; preserving the integrity of the gear.
I could trim down the locking bolt as I didn't have a 22mm bold on hand, just 25mm's. OH, in case someone want to critique it: The layers are printed from barrel to barrel. This part will not split like the original.
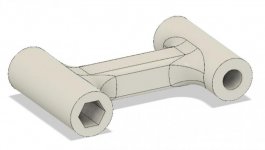
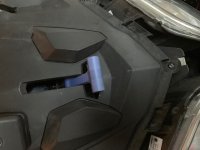
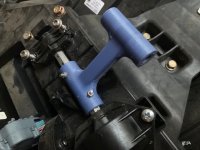
I could easily print more and resell. Not sure how much to sell. Send me a PM if you're interested.
It took me a few hours to design, revise and perfect. The hardest part is getting the old one off. I chose to remove the small end with the magnet; preserving the integrity of the gear.
I could trim down the locking bolt as I didn't have a 22mm bold on hand, just 25mm's. OH, in case someone want to critique it: The layers are printed from barrel to barrel. This part will not split like the original.
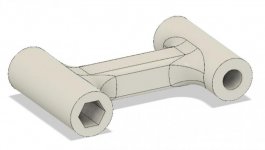
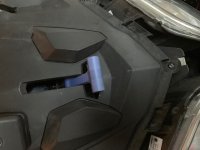
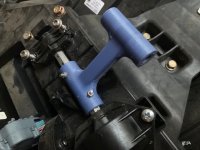